
GRO Restart™ – Wiederanlauf der Produktion nach Störung oder Betriebsunfall
Systematisch handeln. Stabil produzieren. Für zukünftige Krisen gewappnet.
GetRealOpti unterstützt Industrieunternehmen nach technischen Ausfällen, Zwischenfällen oder Arbeitsunfällen mit einem strukturierten Neustart: Ursachenanalyse, TPM-Inspektionen, gezielte Sofortmaßnahmen, Risikobewertung sowie Umsetzung von Notfallplänen und Checklisten. Unser Ansatz basiert auf den internationalen Normen ISO 9001, ISO 45001, ISO 14001 sowie den Prinzipien von Lean Management und TPM. Das Ergebnis: Ein schneller, aber durchdachter Wiederanlauf der Produktion, nachhaltige Fehlervermeidung und mehr Sicherheit für die Zukunft.
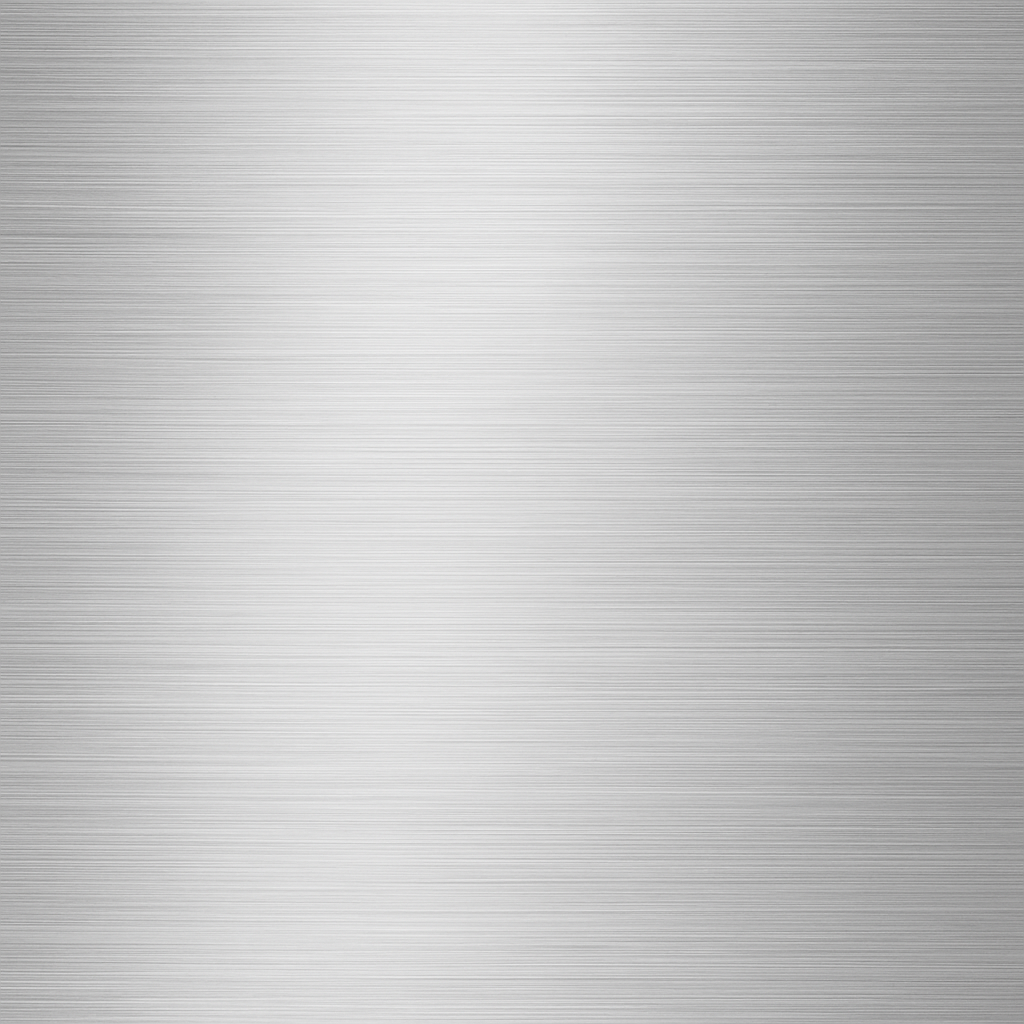
Warum ein Produktions-Restart mehr ist als nur ein Neustart
Ein Ausfall, Unfall oder schwerwiegender Zwischenfall in der Produktion ist kein rein technisches Problem – sondern ein Wendepunkt. Wer in einem solchen Moment einfach „weitermacht“, ohne die Ursache zu beseitigen, riskiert Wiederholungen, Folgeschäden und langfristige Instabilität.
Ein ungeplanter Stillstand betrifft nicht nur Maschinen:
➡️ Er offenbart Schwächen in Prozessen, Organisation und Instandhaltung
➡️ Führt zu Stress, Fehlern und provisorischen Lösungen
➡️ Gefährdet Sicherheit, Produktqualität und Kundenvertrauen
➡️ Und verursacht Kosten – Zeit, Geld und oft mehr, als auf den ersten Blick sichtbar ist
Typische Folgen nicht analysierter Zwischenfälle:
Wiederkehrende Ausfälle – weil die Ursache nicht behoben wurde
Rücksendungen und Reklamationen – durch mangelhafte Qualitätskontrolle
Verlust von Prozesswissen – durch fehlende Dokumentation und Analyse
Überlastung des Teams – ohne Schulungen, Pläne und Checklisten
Unser Ansatz: Technische Ursachenanalyse + TPM + ISO-konforme Absicherung
GRO Restart™ ist kein schneller Reset – sondern ein strukturierter Interventionsprozess.
Wir kombinieren Ursachenanalyse (RCA, 5Why), Sofortmaßnahmen, sicheres Wiederanfahren und nachhaltige Prozesssicherung in einem ganzheitlichen Service:
✅ Schnelle Reaktion innerhalb von 24 Stunden
✅ Ursachenanalyse nach TPM, RCA, ISO 9001 / 45001
✅ Dokumentation mit Fotos, Prozessmaps und Risikoanalysen
✅ Kontrollierte Wiederaufnahme der Produktion – sicher und überwachbar
✅ Schulung des Teams und Prävention vor Wiederholungen
Die konkreten Ergebnisse?
📉 Weniger Fehler und Reparaturkosten
📈 Höhere Stabilität, Sicherheit und Qualität
🧠 Klarheit über die Ursache und gezielte Maßnahmen
🛡️ Mehr operative Widerstandsfähigkeit und Einsatzbereitschaft
Warum GetRealOpti?
Denn echte operative Stabilität beginnt nicht mit „Wird schon irgendwie gehen“.
GRO Restart™ bedeutet: Ursachen erkennen, das System absichern, das Team vorbereiten – mit praxisnaher Expertise und wirksamen Methoden.
Wenn Ihre Produktion durch Technik, Mensch oder Organisation gestört wurde – ist dieser Service der erste Schritt zurück zur vollen Einsatzbereitschaft.
GRO Restart™ – Wiederanlauf der Produktion nach Störung oder Betriebsunfall
🧭 Phase 0 – Meldung und schnelle Situationsbewertung
Eine effektive Reaktion auf einen Ausfall oder Vorfall beginnt mit einer präzisen Einschätzung der Lage. In dieser Phase werden noch keine operativen Maßnahmen ergriffen – im Fokus steht die Erfassung aller relevanten Informationen, die Risikobewertung und die strukturierte Einsatzvorbereitung.
So stellen wir sicher, dass unser Team innerhalb von 24 Stunden mit einem klaren Verständnis der Gefahrenlage und operativen Anforderungen vor Ort ist.
✅ Erfassung der Ausfall- bzw. Vorfallmerkmale: Art, betroffener Bereich, Auswirkungen auf die Produktion
✅ Einstufung der Kritikalität: vollständiger Stillstand, Teilfunktionsverlust, Risiko für Personen oder Umwelt
✅ Kontaktaufnahme mit der verantwortlichen Ansprechperson und Festlegung eines Koordinationspunktes vor Ort
✅ Vorbereitung des passenden Equipments, der Einsatzdokumente, Formulare und eines erfahrenen Einsatzteams
✅ Anfahrtsplanung und Absicherung des Gefahrenbereichs – gemäß BGV-, TPM- und ISO-45001-Vorgaben
📏 Standards und Vorgehensweise:
📌 ISO 9001 – Steuerung und Überwachung des Interventionsprozesses
📌 ISO 45001 – Gefährdungsermittlung und Risikominimierung für Team und Unternehmen
📌 TPM – Einbindung des Bedienpersonals in die sichere Wiederinbetriebnahme
🔍 Ergebnis: Innerhalb von 24 Stunden ist unser Einsatzteam einsatzbereit – mit einem vollständigen Lagebild, passender Ausrüstung und einem klaren Handlungsplan. Das reduziert Stillstandszeiten, verhindert operative Fehler und schafft bereits beim Erstkontakt Vertrauen.
🔍 Phase 1 – Ursachenanalyse und Fehlerdiagnose
Nach der Stabilisierung der Situation und dem ersten Neustart ist der nächste entscheidende Schritt die Ermittlung der tatsächlichen Ursache des Vorfalls. Es reicht nicht aus, die Symptome zu beseitigen – wir müssen verstehen, was genau versagt hat und warum. Nur so können nachhaltige Maßnahmen ergriffen werden, die ein erneutes Auftreten des Problems verhindern.
Wir verwenden bewährte Analysemethoden aus Qualitätsmanagement und Instandhaltung, darunter RCA (Root Cause Analysis), 5 Why und FTA (Fault Tree Analysis) – jeweils angepasst an die Komplexität der Situation.
✅ Technische Inspektion des Schadbereichs – Analyse von Anlagen, Verbindungen, Steuerkreisen
✅ Durchsicht von Unterlagen: Wartungsprotokolle, Störungsmeldungen, SPS-Daten
✅ Ermittlung der primären Fehlerursache – ob technisch, organisatorisch, prozessual oder menschlich
✅ Verknüpfung mit Folgeeffekten – Qualitätseinbußen, Leistungsverlust, Sicherheitsrisiken
✅ Gespräche mit dem Personal, das unmittelbar beteiligt oder betroffen war
📏 Standards und Methodik:
📌 ISO 9001 – Analyse von Abweichungen und Korrekturmaßnahmen
📌 ISO 45001 – Untersuchung sicherheitsrelevanter Auswirkungen
📌 TPM – Einbindung von Bedienern in die Ursachenidentifikation und Prävention
🔍 Ergebnis: Eine klare und nachvollziehbare Definition der Hauptursache sowie ihrer Zusammenhänge mit anderen Bereichen. Auf dieser Basis lassen sich nicht nur technische Mängel beheben, sondern auch strukturelle Schwachstellen dauerhaft eliminieren und die Betriebsstabilität stärken.
♻️ Phase 2 – Sofortmaßnahmen und kontrollierter Produktions-Restart
Nach der Ursachenanalyse folgt die temporäre Wiederherstellung der Betriebsfähigkeit, um Produktionsausfälle zu minimieren und die Prozesskette so schnell wie möglich wieder in Gang zu setzen. Ziel ist nicht die vollständige Reparatur, sondern ein sicherer und überwachter Neustart im Notfallmodus.
Wir implementieren temporäre Lösungen wie Bypässe, Notfallersatzteile oder manuelle Steuerungen – stets gemäß technischer Dokumentation und unter Einhaltung der Sicherheitsvorgaben.
✅ Wiederherstellung der minimalen Funktionalität – auch bei eingeschränktem Betrieb
✅ Temporäre Umgehungslösungen (Bypässe) oder manuelle Steuerung mit Sicherheitsfreigaben
✅ Überwachung kritischer Prozessparameter während des Neustarts
✅ Kennzeichnung und Absicherung der Gefahrenbereiche gemäß ISO 45001
✅ Zusammenarbeit mit dem Bedienpersonal – gemäß TPM-Prinzipien und Sicherheitskultur
📏 Normen und Methoden:
📌 ISO 45001 – Sicheres Arbeitsumfeld, Risikomanagement
📌 TPM – Autonomous Maintenance – Einbindung der Mitarbeiter in kontrollierte Neustarts
📌 ISO 9001 – Sicherung der Produktqualität auch im Notbetrieb
🔍 Ergebnis: Die Produktion wird in einem begrenzten, aber sicheren Rahmen wieder aufgenommen. Qualität und Risiken bleiben unter Kontrolle, während Zeit für nachhaltige Reparaturen gewonnen wird – ohne weitere Stillstandsverluste.
🗂️ Phase 3 – Ereignisdokumentation und Datenanalyse
Nach der Erstreaktion ist eine gründliche Dokumentation des Vorfalls entscheidend. Nur wer versteht, was, wann und warum passiert ist, kann nachhaltige Maßnahmen ableiten und zukünftige Risiken systematisch ausschließen.
Wir erstellen eine umfassende Störungs- oder Unfallanalyse, kombiniert mit visueller Dokumentation, Prozessabbildung und zeitlicher Analyse. Gleichzeitig überprüfen wir die bestehenden Arbeitsanweisungen, Notfallprozeduren und Reaktionsabläufe auf Schwächen.
✅ Erstellung eines Störungs- oder Unfallberichts – inklusive Fotos, Prozesskarten, Zeitlinien
✅ Überprüfung bestehender Anweisungen, Ablaufschemata und Checklisten
✅ Identifikation von organisatorischen Fehlern und Systemlücken
✅ Bewertung der Wirksamkeit bestehender Kontrollmechanismen
✅ Vorbereitung der Datenbasis für FMEA / RCA / interne Audits
📏 Standards und Methoden:
📌 ISO 9001 – Dokumentation von Abweichungen und Korrekturmaßnahmen
📌 ISO 45001 – Ursachenanalyse und Aktionsplanung nach Vorfällen
📌 TPM – Verlustanalyse und Ursachenforschung (Root Cause Analysis)
🔍 Ergebnis: Eine vollständige Dokumentation schafft Transparenz über den Vorfallverlauf und deckt systemische Schwächen auf. Sie bildet die Grundlage für dauerhafte organisatorische, technische und prozessuale Verbesserungen – zur nachhaltigen Risikominimierung.
🛠️ Phase 4 – Empfehlungen für dauerhafte Maßnahmen und Prävention
Nach der Ursachenanalyse liegt der Fokus auf nachhaltigen Lösungen, um Wiederholungen zu vermeiden und die Systemstabilität zu erhöhen. Wir erarbeiten eine konkrete Liste von technischen, organisatorischen und prozessorientierten Präventivmaßnahmen – praxisnah und umsetzbar.
✅ Maßnahmenliste zur dauerhaften Beseitigung von Fehlerursachen (technisch, organisatorisch, prozedural)
✅ Vorschläge zur Anpassung der Dokumentation: Arbeitsplatzanweisungen, Checklisten, Wartungspläne
✅ Optional: Implementierung von TPM, 5S oder internen Prozess-Audits, wenn Ursachen auf das Instandhaltungs- oder Betriebsmanagement zurückzuführen sind
✅ Abstimmung mit den Abteilungen: Produktion, Instandhaltung, Qualität und Arbeitssicherheit
✅ Priorisierung der Maßnahmen mit Aufwand-Nutzen-Bewertung
📏 Standards und Vorgehensweise:
📌 ISO 9001 – Fehlervermeidung durch systematische Prozessverbesserung
📌 TPM – Vermeidung von Ausfällen durch präventive Instandhaltung
📌 Lean / 5S – Standardisierung und Ordnung am Arbeitsplatz
🔍 Ergebnis: Ein konkreter Maßnahmenplan mit hoher Umsetzbarkeit – für mehr Sicherheit, Stabilität und operative Zuverlässigkeit im laufenden Betrieb.
🎓 Phase 5 – Schulung des Teams und Erhöhung der operativen Einsatzbereitschaft
Ein Zwischenfall ist nicht nur ein Moment für Reparaturen – sondern auch eine Gelegenheit zur Weiterbildung. Nach der Stabilisierung der Situation vermitteln wir dem Team Wissen, Tools und Verfahren, um die zukünftige Reaktionsfähigkeit zu verbessern und Wiederholungen zu vermeiden.
✅ Schulung des Produktions- und Instandhaltungsteams basierend auf dem konkreten Vorfall
✅ Übergabe von Checklisten, Notfallverfahren und Reaktionswerkzeugen
✅ Aufzeigen konkreter Verbesserungsmöglichkeiten im Bereich Sicherheit und Qualität
✅ Gespräche mit Mitarbeitenden, Sammlung von Beobachtungen und gemeinsame Lösungsfindung
✅ Verankerung von TPM-Grundsätzen und Best Practices im Team
📏 Standards und Vorgehensweise:
📌 ISO 45001 – Bewusstsein für Gefahren stärken, Kompetenzen gezielt aufbauen
📌 TPM / Lean – Einbindung der Mitarbeitenden in Wartung und kontinuierliche Verbesserung
📌 Krisenpsychologie – Schulung nach einem belastenden Vorfall als Teil der Stabilisierung
🔍 Ergebnis: Das Team kennt nicht nur die Ursache – es kann gezielt reagieren, Wiederholungen vermeiden und fühlt sich verantwortlich für die Prozessstabilität.
🧪 Phase 6 – Validierung und Abschluss der Maßnahmen
Nach Umsetzung aller Sofort- und Präventivmaßnahmen erfolgt die strukturierte Abschlusskontrolle. Ziel: Sicherstellen, dass alle Risiken beseitigt wurden, der Betrieb stabil läuft – und die Organisation aus dem Vorfall gelernt hat.
✅ Finalkontrolle der Sicherheitsstandards und Normkonformität (gemäß ISO 9001 / 45001)
✅ Technische Abnahme, Dokumentation und Unterschrift des Abschlussprotokolls
✅ Besprechung offener Punkte und Restmaßnahmen mit dem Kunden
✅ Feedbackrunde zur Zusammenarbeit, Transparenz über mögliche Schwachstellen
✅ Vorbereitung auf optionale Folgeangebote (z. B. GRO Risk™, GRO Clean™, GRO Check360™)
📏 Standards und Vorgehensweise:
📌 ISO 9001 / 45001 – formalisierter Abschluss, Risikobewertung und Wirksamkeitskontrolle
📌 TPM – langfristige Betriebssicherheit durch systematische Validierung
📌 Lean / KVP – Erkennen von strukturellen Schwächen und Schließen der Lücken
🔍 Ergebnis: Der Vorfall ist nicht nur gelöst, sondern auch strukturell verarbeitet. Die Organisation erhält Klarheit, Sicherheit und dokumentiertes Wissen für zukünftige Resilienz.
🔄 Zusatzleistungen und langfristige Zusammenarbeit
Eine Störung ist kein Ende – sondern der Startpunkt für bewusstes, robustes und proaktives Operieren. Nach der Stabilisierung bieten wir gezielte Wege zur Weiterentwicklung, um Prozesse abzusichern, Organisationsresilienz aufzubauen und eine Kultur der kontinuierlichen Verbesserung zu etablieren.
✅ GRO Risk™ – umfassende Analyse operativer Risiken und Einführung systemischer Schutzmaßnahmen
✅ GRO Clean™ – professionelle Reinigung und TPM-Regeneration kritischer Anlagen (z. B. Lackieröfen, Fördertechnik)
✅ GRO Check360™ – ganzheitliches Audit (technisch, organisatorisch, qualitativ) mit konkreten Optimierungsvorschlägen
✅ GRO System™ – strukturierte Optimierung von Produktionsprozessen: Fluss, Qualität, Maschinen, Team
✅ Operative Schulungen und Einführung von Arbeitsstandards – Aufbau von Effizienz und Handlungssicherheit im Team
📏 Standards und Vorgehensweise:
📌 ISO 9001 / 14001 / 45001 – kontinuierliche Verbesserung und Systemstabilität
📌 TPM + Lean – standardisiertes Management von Wartung und Verlustbeseitigung
📌 GRO System™ – unsere eigene Methodik zur vollständigen Prozessoptimierung auf Produktionsebene
🔍 Ergebnis: Statt zurück in den alten Zustand – entwickelt sich die Organisation auf das nächste operative Level. Eine langfristige Zusammenarbeit mit GetRealOpti bedeutet Stabilität, Vorhersehbarkeit und messbare Effizienzsteigerung.
🧩 Störung? Unfall? Produktionsausfall?
GRO Restart™ ist nicht nur eine Reaktion – sondern ein systematischer Weg zur nachhaltigen Betriebssicherheit.
📌 Wenn die Produktion steht, reicht ein schneller Neustart nicht aus. Wir identifizieren die Ursachen, analysieren die Daten, dokumentieren den Vorfall und liefern gezielte Präventionsmaßnahmen – damit sich der Fehler nicht wiederholt.
👉 Unser strukturiertes Vorgehen umfasst: Vor-Ort-Inspektion, Ursachenanalyse (RCA, 5Why), Risikobewertung, Fotodokumentation, Handlungsempfehlungen und Schulung des Teams.
Wir setzen nicht einfach den Betrieb fort – wir schaffen operative Stabilität und ISO-konforme Sicherheit.
🔧 Und wenn gewünscht – unterstützen wir Ihr Team direkt vor Ort mit Checklisten, klaren Arbeitsanweisungen und praxisnahen Lösungen.
📞 Jetzt unverbindlich anfragen oder einen kostenlosen Erstcheck sichern:
🔧 Zusätzliche Dienstleistung: GRO Risk™ – Risikobewertung für Technik, Organisation und Sicherheit
Für Unternehmen, die Risiken nicht erst dann sehen wollen, wenn sie sich bereits verwirklichen – sondern frühzeitig erkennen, bewerten und vermeiden möchten.
Im Rahmen der Analyse prüfen wir technische Schwachstellen, organisatorische Lücken und sicherheitsrelevante Faktoren – bevor es zu Ausfällen, Unfällen oder Qualitätsverlusten kommt. Jeder kritische Punkt wird visuell dokumentiert und in einem strukturierten Risikobericht bewertet – mit klaren Prioritäten und Handlungsempfehlungen.
Der Audit umfasst u. a.: Prozessparameter und Produktionsstabilität, sicherheitsrelevante Schwächen, organisatorische Risiken, Fehlerquellen, ISO-Konformität (9001, 14001, 45001), TPM-Potenziale sowie Notfallbereitschaft.
🎯 Ergebnis: Ein vollständiger Risikobericht mit Fotodokumentation, Ursachenanalyse und gezielten Empfehlungen – als Basis für präventive Maßnahmen und stabile Abläufe.
Was verändert sich, wenn man nach einem Zwischenfall nicht nur neu startet – sondern den Prozess langfristig absichert?
Viele Unternehmen konzentrieren sich nur auf das Wiederanlaufen der Maschinen – doch die wahren Kosten eines Vorfalls liegen nicht nur im Stillstand, sondern in fehlender Analyse, wiederkehrenden Problemen und Qualitätsverlust. GRO Restart™ ist systematische Unterstützung nach einem Zwischenfall – von der Dokumentation über Ursachenanalyse bis hin zu klaren Empfehlungen, die künftige Krisen verhindern.
✅ Ursachenanalyse statt Symptombehandlung – mit Fotodokumentation, Zeitachsen und Erkennung von Lücken in Prozessen und Zuständigkeiten.
✅ Unfall- und Störungsdokumentation nach ISO-Standards – visuell, nachvollziehbar, auditfähig.
✅ Konkrete Präventionsmaßnahmen – technisch, organisatorisch und prozessbezogen.
✅ Schulung des Teams – mit Checklisten, Tools und klaren Reaktionsstrategien für vergleichbare Situationen.
🧠 Es bleibt nicht bei der Analyse – wir stärken die operative Resilienz: 📋 neue Anleitungen, 🛠️ strukturierte Abläufe, 📉 weniger Wiederholungen und weniger Reaktionsdruck.
📊 Ergebnis: Ein stabiler Prozess, Audit-Bereitschaft, ein geschultes Team mit klarem Verständnis – und ein Unternehmen, das nicht nur reagiert, sondern strukturell vorsorgt.
Kurz gesagt: Wir setzen nicht nur den Prozess zurück – wir sichern ihn, bevor der nächste Fehler passiert.
❓ Häufig gestellte Fragen (FAQ)
❓ Muss ein Neustart der Produktion nach einem Zwischenfall immer mit langen Stillständen verbunden sein?
Nicht unbedingt. Entscheidend ist eine schnelle Situationsbewertung, ein klarer Handlungsplan und ein Team, das weiß, was zu tun ist. Mit GRO Restart™ kann die Produktion je nach Vorfall, Schadensumfang und Teamverfügbarkeit oft innerhalb von 1–3 Tagen sicher wieder aufgenommen werden.
❓ Wann sollte GetRealOpti gerufen werden?
Bei einem Unfall, Brand, Chemieunfall, Produktionsstillstand oder einer kritischen technischen Situation. Auch dann, wenn der akute Vorfall bereits „gelöst“ scheint, aber unklar ist, ob ein sicherer Betrieb möglich ist. GRO Restart™ bedeutet nicht nur Reparatur – sondern auch präventive Absicherung gegen Wiederholungen.
❓ Was umfasst die Leistung GRO Restart™ konkret?
– Analyse der Zwischenfallursache und technische Bewertung
– Planung eines sicheren Wiederanlaufs (technisch und organisatorisch)
– Umsetzung sofortiger Notfallmaßnahmen
– Schulung des Teams und Checklisten für die ersten Tage
– Dokumentation und Empfehlungen für zukünftige Sicherheit
❓ Wie lange dauert ein Restart?
Je nach Schwere des Vorfalls:
– 1 Tag – bei kleineren Stillständen oder organisatorischen Problemen
– 2–3 Tage – bei technischen Ausfällen, die Inspektionen, Reinigung und Reorganisation erfordern
– >3 Tage – bei größeren Schäden, komplexen Anlagen oder wenn mehrere Arbeitsbereiche betroffen sind
❓ Kann der Restart mit anderen Leistungen kombiniert werden?
Ja – sinnvoll ist die Kombination mit:
– GRO Check360™ – Technischer Audit & Prozessbewertung
– Einführung von Sicherheits-Checklisten und Mitarbeiterschulungen
– Bewertung chemischer und organisatorischer Risiken (z. B. nach ISO 45001 / SDS)
– GRO Risk™ – Eliminierung struktureller Schwachstellen für die Zukunft
🏆 Warum GetRealOpti?
Weil wir Produktion als ein System verstehen – und nicht als eine Summe einzelner Probleme.
Hinter jeder Reklamation steckt ein Prozess.
Und hinter jedem Prozess: konkrete technische, organisatorische oder materialbedingte Ursachen.
Das Team von GetRealOpti vereint über 15 Jahre operative Erfahrung mit tiefgreifender Expertise in der Prozessanalyse, Maschinenoptimierung, TPM und Lean-Implementierung – direkt auf dem Shopfloor
🔥 Krisenerprobte Erfahrung
Wir standen in einer Halle mit 600 Litern Lösungsmittel auf dem Boden – nur 15 Meter vom aufgeheizten Ofen entfernt.
Wir haben Brände gesehen, bei denen Flammen 30 Meter hoch aus dem Kamin schlugen.
Wir waren vor Ort, als es zu einem tödlichen Unfall in der Produktion kam – und wissen, was ein echter Ernstfall bedeutet.
Wir kennen den Druck, wenn jede Stunde Stillstand tausende Euro kostet – und noch mehr: Leben, Gesundheit und Reputation stehen auf dem Spiel.
⚙️ Handeln statt Panik
Sie brauchen keinen weiteren Bericht für die Schublade –
Sie brauchen ein Team, das weiß, was zu tun ist, wenn die Kontrolle verloren geht.
Wir analysieren die Ursache, sichern den Neustart ab und implementieren sofortige sowie präventive Maßnahmen.
🤝 Verständnis für Menschen und Druck
Wir wissen, wie die Augen eines Mitarbeiters nach einem Unfall aussehen.
Wir kennen die Fragen des Managements, wenn es keine Antworten gibt.
Wir arbeiten mit dem Team – nicht gegen es. Und wir bringen Stabilität zurück, wo zuvor Chaos herrschte.
🛠️ Was uns auszeichnet
GetRealOpti ist kein klassisches Beratungsunternehmen – sondern operativer Support, direkt mit Ihrem Team umgesetzt.
Unsere Module liefern messbare Ergebnisse in nur 30–90 Tagen:
GRO Check360™ – technische Bewertung und Prozessanalyse direkt vor Ort
GRO Clean™ – professionelle Reinigung und TPM-Regeneration für industrielle Anlagen
GRO Restart™ – schnelle Reaktion und sicherer Wiederanlauf nach Zwischenfällen
GRO Risk™ – gezielte Risikoanalyse und operative Absicherung Ihrer Produktion
GRO System™ – Optimierung nach Lean, TPM, 5S und gezielter Verlustreduzierung
Schulungen & Checklisten – direkt am Arbeitsplatz eingeführt
Maschinen-Start & Tuning – angepasst an reale Bedingungen (Mikrostillstände, Materialfluss)
TPM-Einführung – systematische Instandhaltung mit –40 % weniger Ausfällen
Langfristige Begleitung – von Standardisierung bis zum vollständigen Managementsystem
📋 Ergebnisse, die bleiben
Wir lassen Sie nicht mit einer leeren Präsentation zurück.
Wir hinterlassen einen Plan, klare Verfahren, Checklisten – und ein Team, das weiß, was zu tun ist.
🎯 Das Ergebnis?
Schnellere Rückkehr zur Produktion
Geringeres Wiederholungsrisiko
Höhere Prozessstabilität und Qualität
Ein Team, das bewusst und verantwortungsvoll handelt